Continuous improvement involves identifying, analyzing, and improving business processes and strategies to increase efficiency, productivity, and profitability. It is crucial for long-term success in any industry or business. Failure to continuously improve risks causing a business to fall behind its competitors.
This article outlines several continuous improvement techniques. By implementing these strategies, businesses can achieve sustainable growth and success.
Jump To Section
Creating a Culture of Continuous Improvement
To implement continuous improvement, you need to create a culture that supports it. This means involving everyone in the company, from leaders and teams to every process and work process. By making continuous improvement a part of your culture, you can identify and eliminate inefficiencies, stay ahead of the competition, and drive positive change.
Creating a culture of continuous improvement requires a top-down approach, with leaders setting the tone and empowering employees to participate in the process. Leaders should communicate the importance of continuous improvement and provide the necessary resources and training to support it. They should also encourage employees to identify improvement opportunities and provide a forum for sharing ideas.
To involve everyone in the process, you can use various improvement techniques such as conducting regular team meetings, brainstorming sessions, and Gemba walks. These techniques can help identify inefficiencies and areas for improvement, and involve everyone in the process of finding solutions.
By creating a culture of continuous improvement, you can achieve a range of benefits such as improved efficiency, reduced costs, increased customer satisfaction, and better employee engagement. It also helps you stay ahead of the competition by continuously improving your products, services, and processes.
Implementing Continuous Improvement Techniques
There are many improvement strategies that you can use to achieve continuous improvement. The most popular methodologies include Kaizen, Six Sigma, and PDCA. Each of these methods focuses on improving the quality of your product or service by eliminating waste and reducing variation in processes.
Benefits of Continuous Improvement
Continuous improvement is a powerful tool for organizations to achieve their goals and objectives. Here are some of the benefits of continuous improvement:
- Increased customer satisfaction: Continuous improvement helps you identify and address customer needs and expectations. By making incremental improvements, you can improve the quality of your product or service, reduce defects, and improve customer satisfaction.
- Reduced costs: Continuous improvement helps you identify and eliminate waste in your processes. By reducing waste, you can improve efficiency, reduce costs, and increase profitability.
- Improved efficiency: Continuous improvement helps you identify and eliminate inefficiencies in your processes. By improving efficiency, you can reduce cycle times, improve productivity, and increase throughput.
- Better employee engagement: Continuous improvement involves everyone in the organization, from leaders and teams to every process and work process. By involving employees in the process of identifying improvement opportunities and implementing changes, you can improve employee engagement and morale.
- Competitive advantage: Continuous improvement helps you stay ahead of the competition by continuously improving your products, services, and processes. By making incremental improvements, you can achieve a competitive advantage and drive business results.
In summary, continuous improvement is a powerful tool for organizations to achieve their goals and objectives. By identifying improvement opportunities and implementing changes in a structured and methodical way, you can achieve a range of benefits such as increased customer satisfaction, reduced costs, improved efficiency, better employee engagement, and competitive advantage.
Strategies for Continuous Improvement
1. Implement Kaizen methodology
Kaizen is a Japanese term that means “change for the better.” It is a methodology that focuses on making continuous improvements to processes by involving everyone in the organization.
2. Use Six Sigma to reduce variation in processes
Six Sigma is a data-driven methodology that aims to eliminate defects in processes by reducing variation. It uses statistical analysis to identify and eliminate the root causes of problems.
3. Conduct regular process audits
Regular process audits can help identify inefficiencies and areas for improvement. By reviewing processes on a regular basis, you can ensure that they are running smoothly and identify opportunities for improvement.
4. Implement PDCA (Plan-Do-Check-Act) cycle
The PDCA cycle is a continuous improvement model that involves four stages: planning, doing, checking, and acting. It is a structured approach to making improvements to processes.
5. Use Lean improvement techniques to eliminate waste
Lean is a methodology that aims to eliminate waste in processes. It involves identifying and eliminating non-value-added activities to improve efficiency and reduce costs.
6. Conduct customer satisfaction surveys
Customer satisfaction surveys can provide valuable feedback on the quality of your product or service. By using this feedback to make improvements, you can improve customer satisfaction and loyalty.
7. Use data analysis to identify improvement opportunities
Data analysis can help identify trends and patterns that can be used to make improvements. By analyzing data on a regular basis, you can identify improvement opportunities and make data-driven decisions.
8. Implement a culture of continuous improvement
A culture of continuous improvement involves making improvement a part of the organization’s values and beliefs. By encouraging employees to identify improvement opportunities and make changes, you can achieve continuous improvement.
9. Conduct regular training sessions for employees
Regular training sessions can help employees develop new skills and knowledge. This can lead to improved efficiency and better performance.
10. Use Kanban to streamline workflow
Kanban is a visual management tool that can be used to streamline workflow. It involves using cards or boards to track the status of tasks and identify bottlenecks in the process.
11. Conduct regular team meetings to discuss improvement opportunities
Regular team meetings can provide a forum for discussing improvement opportunities and identifying solutions. By involving everyone in the process, you can achieve continuous improvement.
12. Use process mapping to identify inefficiencies
Process mapping involves creating a visual representation of a process. By doing so, you can identify inefficiencies and areas for improvement.
13. Implement Total Quality Management (TQM)
TQM is a management philosophy that aims to improve quality by involving everyone in the organization. It involves a focus on continuous improvement and customer satisfaction.
14. Conduct regular benchmarking to compare performance to industry standards
Benchmarking involves comparing your performance to industry standards. By doing so, you can identify areas for improvement and best practices that can be implemented.
15. Use Root Cause Analysis (RCA) to identify the underlying causes of problems
RCA is a methodology that involves identifying the underlying causes of problems. By doing so, you can implement solutions that address the root cause of the problem.
16. Implement a continuous improvement software tool
Continuous improvement software tools can help track improvement opportunities and monitor progress. They can also provide data analysis and reporting capabilities.
17. Develop a continuous improvement roadmap
A continuous improvement roadmap involves identifying improvement opportunities and prioritizing them based on their impact and feasibility. It provides a structured approach to making improvements.
18. Use brainstorming sessions to generate improvement ideas
Brainstorming sessions can provide a forum for generating improvement ideas. By involving everyone in the organization, you can identify a wide range of improvement opportunities.
19. Conduct regular Gemba walks to observe processes in action
Gemba walks involve observing processes in action. By doing so, you can identify inefficiencies and areas for improvement.
20. Use automation to streamline processes
Automation can be used to streamline processes and reduce manual labor. By automating repetitive tasks, you can improve efficiency and reduce errors.
21. Conduct regular performance reviews
Regular performance reviews can help identify areas for improvement and provide feedback to employees. This can lead to improved performance and better results.
22. Use visual management tools to improve communication
Visual management tools can be used to improve communication and provide real-time feedback. This can help identify inefficiencies and areas for improvement.
23. Conduct regular risk assessments to identify potential issues
Regular risk assessments can help identify potential issues before they become problems. By doing so, you can implement solutions to prevent them from occurring.
24. Use cross-functional teams to identify improvement opportunities
Cross-functional teams can provide a diverse range of perspectives on improvement opportunities. By involving multiple departments in the process, you can achieve more comprehensive solutions.
25. Encourage employee involvement in continuous improvement efforts
Employee involvement is critical to achieving continuous improvement. By encouraging employees to identify improvement opportunities and make changes, you can achieve a culture of continuous improvement.
Example of Continuous Improvement
- Amazon: Amazon is known for its customer-centric approach and obsession with continuous improvement. The company uses customer feedback to drive improvements in its products, services, and processes. For example, Amazon introduced the “1-click” ordering system, which allows customers to make purchases with a single click, reducing the time and effort required to complete a purchase.
- McDonald’s: McDonald’s uses continuous improvement to improve the quality and consistency of its food and service. The company uses a system of “plan-do-check-act” to identify improvement opportunities and implement changes. For example, McDonald’s introduced a system of “made-to-order” food, which allows customers to customize their orders and reduces waste.
- General Electric: General Electric uses continuous improvement to improve its products and services. The company uses a system of “Six Sigma,” which focuses on reducing defects and improving quality. For example, General Electric introduced a system of “lean manufacturing,” which involves identifying and eliminating waste in its manufacturing processes.
- Procter & Gamble: Procter & Gamble uses continuous improvement to improve its products and processes. The company uses a system of “innovation sprints,” which involves rapid prototyping and testing of new ideas. For example, Procter & Gamble introduced the “Swiffer” cleaning system, which was developed through a series of innovation sprints.
- Ford: Ford uses continuous improvement to improve the quality and efficiency of its manufacturing processes. The company uses a system of “Ford Production System,” which focuses on waste reduction and process improvement. For example, Ford introduced a system of “assembly line balancing,” which involves balancing the workload across the assembly line to improve efficiency.
In summary, continuous improvement is a powerful tool for organizations to achieve their goals and objectives. By making small, incremental improvements to products, services, and processes, organizations can achieve significant improvements in efficiency, quality, and customer satisfaction.
Wrapping It Up
In conclusion, continuous improvement is like a journey that never ends. It is an ongoing effort to improve your processes, eliminate waste, and drive positive change within your organization. By implementing continuous improvement techniques and creating a culture of continuous improvement, you can achieve success and stay ahead of the competition.
FAQ
Q: What is a continuous improvement tool?
A: A continuous improvement tool is a resource or methodology used to enhance processes, products, or services over time. These tools help organizations identify inefficiencies and implement strategies for improvement, such as the 5 whys or value stream maps.
Q: How can I start with continuous improvement in my organization?
A: To start with continuous improvement, begin by assessing your current processes. Identify areas for improvement and select appropriate continuous improvement tools and methodologies, such as lean management or the improvement cycle, to implement changes gradually.
Q: What is the role of a value stream map in the improvement process?
A: A value stream map is a visual representation of the steps involved in a process. It helps identify waste and inefficiencies within the current process, allowing teams to focus on areas that require improvement and streamline their operations.
Q: Can you explain the 5 whys technique?
A: The 5 whys is a problem-solving technique that involves asking “why” five times to uncover the root cause of an issue. This continuous improvement technique helps teams understand the underlying problems in their processes and develop effective solutions.
Q: What are some popular continuous improvement methodologies?
A: Some popular continuous improvement methodologies include lean methodology, Six Sigma, and the Plan-Do-Check-Act (PDCA) cycle. These approaches provide structured frameworks for improving productivity and efficiency in business processes.
Q: How do improvement methodologies contribute to productivity?
A: Improvement methodologies enhance productivity by systematically identifying and eliminating waste, optimizing processes, and fostering a culture of ongoing improvement. This leads to better resource utilization and higher-quality output in the production process.
Q: What tools and methods can be used for continuous improvement?
A: Various tools and methods can be used for continuous improvement, such as root cause analysis, process mapping, and performance metrics. These tools help organizations assess their improvement initiatives and track progress over time.
Q: What is the continuous improvement process?
A: The continuous improvement process is an ongoing effort to enhance products, services, or processes. It typically involves identifying areas for improvement, implementing changes, measuring results, and refining processes based on feedback, creating a cycle of ongoing enhancement.
Q: How does lean management relate to continuous improvement?
A: Lean management is a philosophy that focuses on maximizing value while minimizing waste. It is closely related to continuous improvement as it provides tools and techniques to streamline processes and enhance efficiency, ultimately driving improvement initiatives.
Q: What are some steps involved in an improvement project?
A: Steps involved in an improvement project typically include defining the problem, analyzing current processes, developing solutions, implementing changes, and monitoring results. Following these steps ensures a structured approach to achieving continuous improvement.
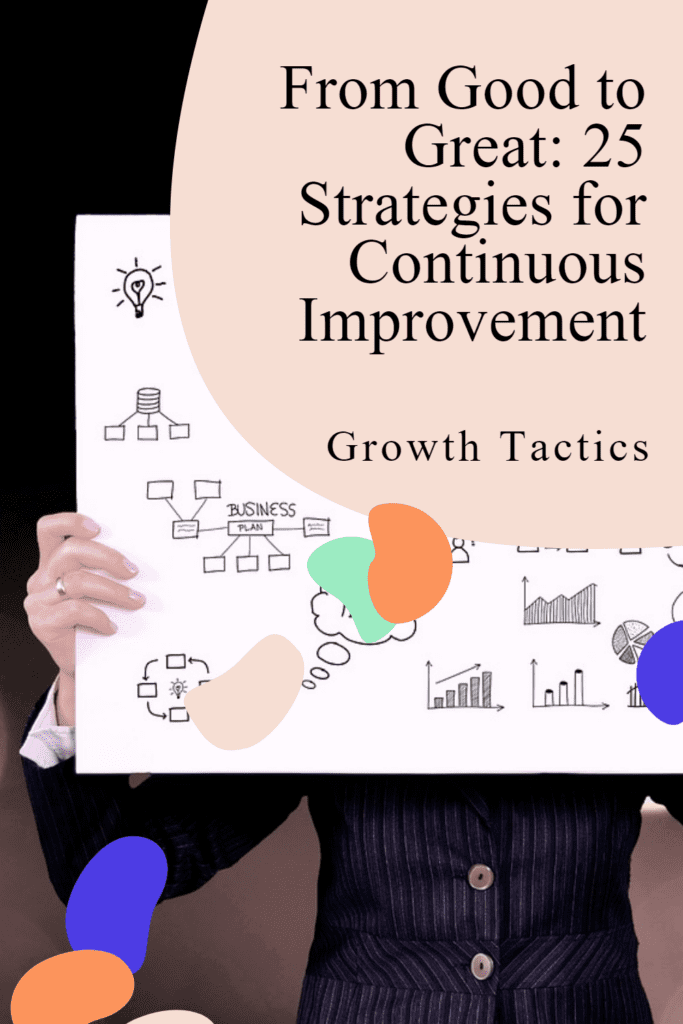