Are you looking to enhance your business operations and drive efficiency?
Look no further!
In this collection of ideas, you’ll find a treasure trove of strategies and suggestions to optimize your processes, reduce waste, and boost productivity.
Whether you’re a small business owner or a team leader, these inspirational ideas will inspire you to take your operations to the next level. Let’s embark on a journey of continuous improvement together!
Jump To Section
Understanding Process Improvement
Process improvement is the practice of identifying and optimizing inefficient processes within a business. By streamlining workflows, reducing waste, and increasing productivity, organizations can deliver higher quality products and services while reducing costs. This leads to a competitive advantage, improved customer satisfaction, and higher employee engagement.
To begin the process improvement journey, businesses must first map out their processes and analyze them for bottlenecks and inefficiencies. Strategies like automation, simplification, and improved communication can then be implemented to drive innovation and achieve better results. Continuous improvement and investment in process improvement tools and methodologies are key to long-term success.
Identifying Inefficiencies
Identifying inefficiencies is a critical step in the process improvement journey. It involves examining business processes to identify areas where bottlenecks and inefficiencies are present. This can be done by mapping out the process, documenting each step, and analyzing the data.
During the analysis, organizations may look for signs of waste, such as redundant or unnecessary steps, delays, errors, or excessive handoffs between team members. They may also consider feedback from employees and customers who interact with the process regularly.
By identifying these inefficiencies, organizations can target specific areas for improvement and devise strategies to streamline the process, reduce waste, and enhance productivity. This helps to drive overall efficiency and effectiveness, ultimately leading to improved business performance and customer satisfaction.
Generating Improvement Ideas
Generating improvement ideas is a crucial part of the process improvement journey. It involves brainstorming and gathering suggestions for enhancing business processes and addressing identified inefficiencies. Here are a few strategies for generating improvement ideas:
- Employee feedback: Encourage employees who are directly involved in the process to share their insights and ideas for improvement. They have valuable firsthand experience and can offer unique perspectives.
- Benchmarking: Look at how other organizations, especially industry leaders, have optimized similar processes. Analyze their best practices and consider adapting them to your own operations.
- Continuous learning and training: Invest in continuous learning opportunities for employees to stay up-to-date with the latest industry trends and advancements. This can inspire new ideas for process enhancements.
- Cross-functional collaboration: Bring together individuals from different departments or teams who have diverse expertise and perspectives. Collaborative brainstorming sessions can generate creative and innovative improvement ideas.
- Process mapping and analysis: Analyze the current process map for gaps, bottlenecks, and areas of inefficiency. This examination can help identify improvement opportunities and generate ideas for streamlining the workflow.
- Technology and automation: Explore how technology can be leveraged to automate manual or repetitive tasks, streamline workflows, and eliminate errors. Automation can lead to significant productivity gains and process improvements.
By actively seeking out improvement ideas, organizations can tap into the collective knowledge and creativity of their employees and stakeholders, leading to a robust list of ideas that can be prioritized and implemented for process enhancement.
Implementing Process Improvement Strategies
Implementing process improvement strategies is the final step in the process improvement journey, and it is where ideas for efficiency and productivity are turned into actions. Here are some key steps to consider when implementing process improvement strategies:
- Prioritize actions: Prioritize the improvement ideas generated from the analysis of inefficiencies and inefficiencies flagged in the process. This can be done by considering factors such as expected impact, effort required, and available resources.
- Develop an action plan: Develop a detailed action plan for the prioritized improvements, including timelines, responsible parties, and resources required. This plan should be robust and adaptable to changes that may arise during the execution of the project.
- Assign responsibilities and accountabilities: Assign specific tasks and responsibilities to team members who are well-placed to take ownership of the implementation and monitor progress towards the improvement goals.
- Measure effectiveness: Define key metrics and performance indicators to measure the effectiveness of the implemented process improvements. Regularly track progress to ensure that the strategies are delivering the expected results.
- Continuous improvement: Once the process improvement strategies are implemented, keep looking for ways to further improve the process. The goal is to continuously improve and refine the process to meet evolving business needs and ensure maximum efficiency and productivity.
By following these steps, organizations can successfully implement process improvement strategies to streamline workflows, reduce waste, and enhance productivity. These efforts can benefit both the business and customers, leading to improved customer satisfaction, employee engagement, and overall business performance.
30 Process Improvement Ideas for Inspiration
Process Analysis
- Standardize workflows and procedures to avoid confusion and streamline operations.
- Conduct regular process audits to identify bottlenecks and areas for improvement.
- Use data analysis to identify patterns and trends that can lead to process optimization.
- Optimize communication channels to ensure smooth information flow within teams and departments.
- Integrate quality control measures to identify and address process gaps or errors.
- Regularly review and update process documentation to ensure accuracy and relevance.
Employee Engagement
- Foster a culture of continuous improvement to encourage employees to seek ways to enhance processes.
- Provide employee training to enhance their skills and knowledge in process improvement techniques.
- Implement a suggestion program to gather ideas for process improvement from employees.
- Encourage cross-functional collaboration to identify opportunities for process improvement.
- Encourage cross-training and knowledge sharing to reduce dependency on specific individuals.
- Foster a positive work environment that supports innovation and experimentation.
- Foster a supportive and open communication culture where employees feel empowered to share their ideas for process improvement.
Automation and Technology
- Implement automation tools or software to reduce manual tasks and increase efficiency.
- Investigate new technologies and tools that can automate or simplify complex processes.
Customer Focus
- Review customer feedback and incorporate their suggestions to enhance customer-focused processes.
Performance Measurement
- Implement problem-solving techniques such as root cause analysis to address recurring issues.
- Allocate resources and allocate dedicated teams for process improvement efforts.
- Set SMART (Specific, Measurable, Achievable, Relevant, Time-bound) goals for process improvement initiatives.
- Engage in benchmarking activities to learn from industry best practices and adopt them into your processes.
- Implement performance measurement systems to track progress and provide feedback for improvement.
- Regularly review and update key performance indicators (KPIs) to align with business goals.
- Implement a continuous improvement feedback loop where progress is assessed, adjustments are made, and continuous improvement is pursued.
- Conduct regular process reviews to identify areas for improvement and implement corrective actions.
Lean Manufacturing
- Embrace lean manufacturing principles to eliminate waste and optimize resources.
- Re-evaluate and refine your supply chain processes to improve efficiency and reduce lead times.
Process Improvement Strategies
- Use project management tools to track progress and identify areas for improvement.
- Implement visual management systems to enhance visibility and transparency in processes.
- Implement a continuous improvement feedback loop where progress is assessed, adjustments are made, and continuous improvement is pursued.
- Celebrate and recognize successful process improvement initiatives to promote a culture of innovation.
Best Practices for Business Process Improvement
There are several best practices to keep in mind when it comes to business process improvement:
- Clearly define objectives: Clearly define the goals and objectives of the process improvement initiative. This ensures everyone involved understands what is trying to be achieved and aligns efforts towards those objectives.
- Involve stakeholders: Involve key stakeholders from different departments and levels within the organization in the process improvement efforts. This ensures diverse perspectives and promotes buy-in and support for the changes.
- Map and analyze processes: Map out and analyze the current processes to identify inefficiencies, bottlenecks, and areas for improvement. Use data and metrics to quantify the impact of the identified issues and prioritize them accordingly.
- Seek employee engagement: Involve employees who are directly involved in the process. Encourage their participation and input, as they often have valuable insights and suggestions based on their day-to-day experiences.
- Set realistic expectations: Set realistic timelines and expectations for the implementation of process improvements. Recognize that change takes time and may encounter obstacles along the way. Being prepared for challenges helps in managing expectations effectively.
- Test and iterate: Pilot the proposed improvements on a smaller scale before implementing them organization-wide. This allows for testing, gathering feedback, and making adjustments as necessary. Iterating on the improvement process helps in refining and optimizing it further.
- Communicate and train: Effective communication and training are crucial for successful process improvement efforts. Clearly communicate the changes to all stakeholders, including employees and customers, and provide adequate training and support to ensure a smooth transition.
- Measure and monitor: Establish key performance indicators (KPIs) and metrics to measure the effectiveness and impact of the implemented process improvements. Regularly monitor these metrics to identify any deviations or areas needing further improvement.
By following these best practices, organizations can maximize the success of their business process improvement initiatives and drive continuous improvement and growth.
Continuous Process Improvement
Continuous process improvement (CPI) is a practice that focuses on identifying and enhancing business processes in an ongoing and iterative manner. Rather than a one-time effort to improve processes, CPI involves a continual effort to refine and optimize them over time.
Some core principles of continuous process improvement include:
- Emphasizing feedback: Soliciting feedback from stakeholders, both internal and external, is critical to identifying process improvement opportunities.
- Data-driven improvement: Objective measurement and analysis of data help organizations evaluate the effectiveness of current processes and identify areas for improvement.
- Continuous tracking: Tracking metrics on an ongoing basis can help organizations identify any deviations from expected performance and address them quickly to maintain efficiency.
- Collaborative approach: Improving and streamlining processes across teams and departments often requires a collaborative approach that involves those most familiar with the processes themselves.
- Cultivating a continuous improvement culture: Regular communication of progress, successes, and setbacks is critical for the successful adoption of a CPI culture that fosters innovation and continuous improvement.
Implementing a CPI program can result in a range of benefits, including cost savings, increased efficiency, reduced cycle times, better customer satisfaction, and reduced errors. Ultimately, it helps organizations stay competitive by enabling them to continuously adapt to changing business environments and customer demands.
Examples of Process Improvement
Process improvement strategies can be highly effective when implemented correctly. Many companies have successfully used various strategies to optimize their operations, reduce waste, and enhance productivity. Here are some real-life examples:
Example 1: Toyota and Lean Manufacturing Principles
Strategy Used: Lean Manufacturing
Toyota is renowned for its implementation of Lean Manufacturing principles, often referred to as the Toyota Production System (TPS). By focusing on eliminating waste, optimizing workflows, and improving overall efficiency, Toyota revolutionized the automotive industry. One specific strategy was the adoption of Just-In-Time (JIT) production, which significantly reduced inventory costs and improved efficiency.
Outcome:
Toyota achieved higher quality products with less waste and lower costs. This methodology also allowed them to respond more flexibly to market demands.
Example 2: General Electric (GE) and Six Sigma
Strategy Used: Performance Measurement and Problem Solving
General Electric (GE) is a prime example of using the Six Sigma methodology for process improvement. Six Sigma focuses on data-driven decision-making to reduce defects and improve quality. GE heavily invested in Six Sigma training and projects across various departments to identify inefficiencies and streamline processes.
Outcome:
General Electric reported savings in the billions of dollars due to reduced inefficiencies and improved process quality. The culture of continuous improvement became ingrained in the organization.
Example 3: Amazon and Automation
Strategy Used: Automation and Technology
Amazon has continuously leveraged automation and advanced technologies to streamline its operations, particularly in its fulfillment centers. For instance, the use of robotic systems to transport items within warehouses has significantly reduced the time required to process and ship orders.
Outcome:
Amazon has been able to provide faster delivery times and handle a greater volume of orders with improved accuracy, significantly enhancing customer satisfaction.
Example 4: Starbucks and Employee Engagement
Strategy Used: Employee Engagement
Starbucks has used employee engagement strategies to improve processes and customer service. They created a feedback loop where employees could share their ideas for process improvement. This includes the Green Apron program, where baristas suggest ways to improve product quality and service.
Outcome:
These initiatives have led to improved employee satisfaction and retention, as well as better customer experiences through consistent service quality and innovation in product offerings.
Example 5: Apple and Continuous Learning
Strategy Used: Continuous Learning and Training
Apple invests heavily in continuous learning and development for its employees. They encourage a culture of constant learning through training programs and innovation labs, enabling employees to stay at the forefront of technology and design.
Outcome:
This strategy has allowed Apple to maintain its status as a market leader in technology and consumer electronics by constantly driving innovation and ensuring high product standards.
Conclusion
In conclusion, the 30 inspirational ideas for process improvement provide a wealth of strategies and approaches to enhance organizational efficiency, effectiveness, and customer satisfaction.
By incorporating these inspirational ideas into their improvement initiatives, organizations can drive positive change, streamline operations, and achieve continuous growth and success.
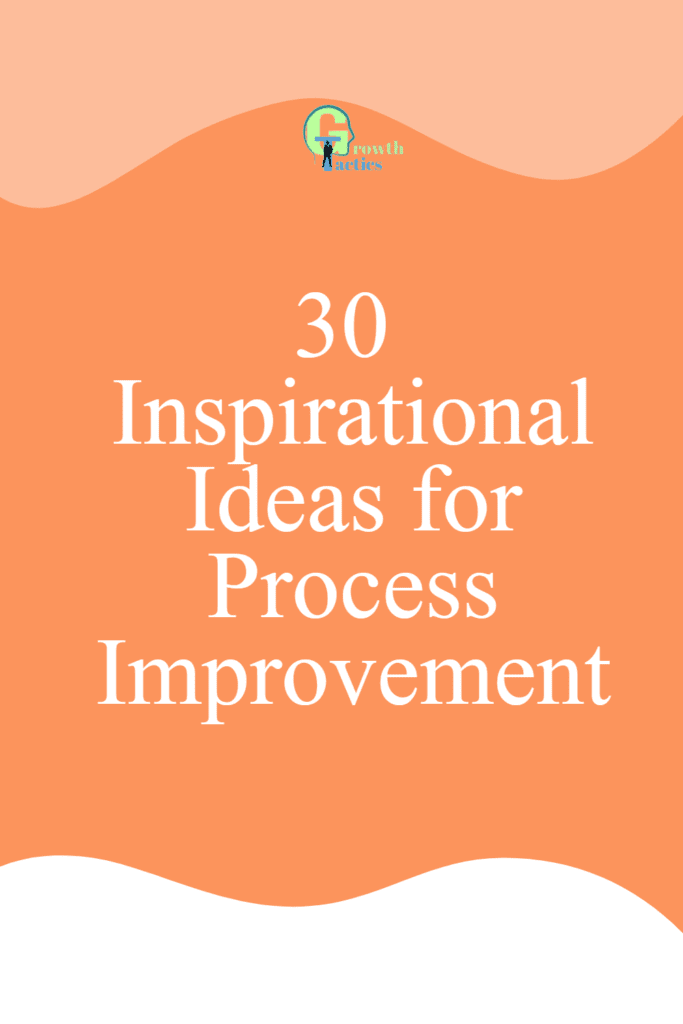